Shelf Life Considerations for Rubber and Silicone
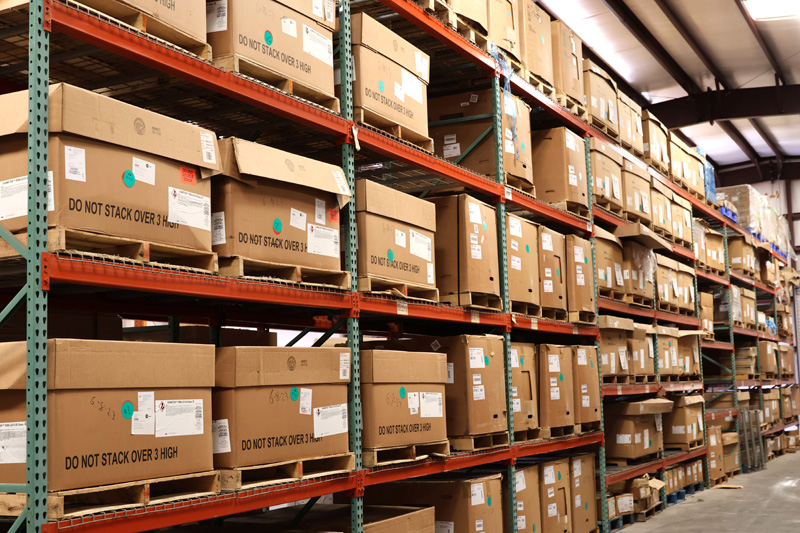
Rubber shelf life refers to the duration during which rubber materials retain their optimal performance and properties when properly stored. It is important to understand and manage the shelf life of rubber products to ensure their reliability and effectiveness in various applications.
Several factors can influence the shelf life of rubber products. These include:
- Rubber Type: Different types of rubber exhibit varying levels of resistance to degradation over time. Understanding the specific characteristics of the rubber used in your products is crucial in determining its expected shelf life.
- Environmental Conditions: Temperature, humidity, exposure to light, and the presence of chemicals or ozone can accelerate the degradation of rubber. Proper storage conditions play a significant role in preserving the integrity of rubber materials.
- Formulation and Additives: The composition of rubber compounds, including additives, fillers, and curing agents, can impact the shelf life. Careful selection of ingredients and formulations is essential for optimizing longevity.
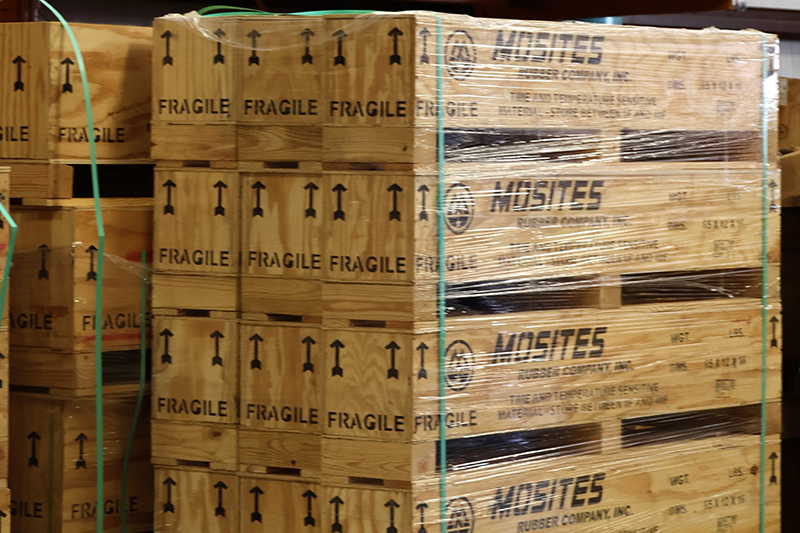
Storage Recommendations
To maximize the shelf life of rubber products, consider the following recommendations for proper storage:
- Temperature and Humidity: Store rubber materials in a cool, dry environment to minimize the effects of heat and moisture. Extremes in temperature and high humidity can accelerate degradation.
- Light Exposure: Protect rubber from direct sunlight and sources of ultraviolet (UV) radiation, as prolonged exposure can lead to premature aging and degradation.
- Chemical and Ozone Exposure: Keep rubber away from chemicals, oils, solvents, and ozone-generating equipment, as these can deteriorate the rubber over time.
- Packaging and Sealing: Seal rubber products in airtight containers or packaging to minimize exposure to air and moisture. Use appropriate barrier materials to prevent degradation.
- Rotation and Inventory Management: Implement a first-in, first-out (FIFO) inventory system to ensure that older rubber materials are used before newer ones. Regularly check and inspect stored rubber products for any signs of deterioration.
Best Practices for Maintaining Product Quality
Adhering to the following best practices can help maintain the quality and extend the shelf life of rubber products:
- Regular Inspection: Periodically inspect stored rubber materials for any signs of degradation, including changes in appearance, texture, or performance. Discard any items that show significant deterioration.
- Testing and Evaluation: Conduct routine quality tests to assess the physical and mechanical properties of stored rubber products. This can help identify any degradation or changes in performance.
- Proper Handling: Follow appropriate handling procedures to prevent unnecessary stress, contamination, or damage to rubber materials.
- Documentation and Tracking: Maintain accurate records of the date of manufacture, storage duration, and other relevant information for proper traceability and shelf life management.